This week, I decided to make a variation of the mold we used last week. My silicone cast had a lot of room for improvement, and I wanted to iterate before I moved along completely from the base design.
I researched some of the possibilites of how I might adjust that design to yield a different kind of actuation. I was particularly interested in the internal restraints I could introduce to the design. In my research, I came across fiber-reinforced actuators in the Soft Robotics Toolkit. These actuators consisted of a flexible bladder that were wrapped with inextensible fibers, or thread, to constrain radial expansion.
The site suggested that the the following arrangement would result in an axial expansion (rather than the typical radial expansion we see in other balloon-like actuators):
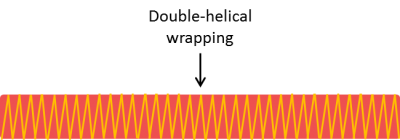
In order to implement this design, I decided to use a two part casting process. Initially, I covered the inner mold from last week in silicone (using less than 5g of mixtures A and B each). I allowed this to cure until the surface was squishy to the touch.
Next, I wrapped thread in a double-helical pattern around the length of the inner mold.
Then, in a fill and degas process similar to the one utilized last week, I placed the inner mold in the outer mold, this time working quickly enough that the mixture was significantly less viscous than last week’s iteration at this stage of fabrication.
I then allowed the whole mold to cure overnight.
[I’ll update with a video, once I’ve tested its behavior with an air pump.]